Methodology
for Validation and Documentation of Vehicle Finite Element Crash ModelS for
Roadside Hardware Applications
ABSTRACT
Researchers
involved in finite element method (FEM) crash simulation of Roadside Hardware need
efficient, validated FE models of vehicles. The National Crash Analysis Center (NCAC) funded
by the US Department of Transportation have
been developing and releasing to the public domain numerous vehicle FE models.
These models are modified and combined with other models to develop specific
simulation scenarios. Users of the models regularly make modifications to the
basic vehicle model according to their particular simulation requirements. A
cooperative effort between the National
Transportation Research Center (NTRC), Oak
Ridge National Laboratory (ORNL), Battelle,
and NCAC was initiated to explore the possibility of updating and enhancing the
kinematic and structural accuracy of these basic vehicle models. This document
outlines the methodology used in evaluating, validating against experimental
data and updating NCAC's Ford F800 Single Unit Truck FE model. A new Hypertext
Markup Language (HTML)-based documentation has been developed to facilitate the
model adoption and understanding of prospective users. The overall methodology
used by the participants - from evaluation to validation to documentation - is
outlined here can be applied to other basic vehicle FE model
currently available to users, and in our opinion could further facilitate
crashworthiness research.
INTRODUCTION
It has become a standard practice in roadside hardware
research to evaluate new and existing designs with computational simulations
using large and complex models based on the Finite Element Method (FEM) [1].
Building a FE model of an entire vehicle
of any kind is a considerable undertaking. A significant technical expertise
and FEM tradecraft is needed to develop a computationally feasible and
practical model that replicates the main kinematics of the vehicle and the
deformation response due to the impact loads.
The most challenging aspect of model
development is the constant tradeoff between the real world complexity of the
vehicle and engineering simplification of its model that should not compromise
the final goal of a sufficiently accurate model suited for its purpose. This
tradeoff process evolves with advances in computing and, therefore, the already
developed models may need to be updated not only to remedy some of their
drawbacks, but also to bring them up to the ever-improving levels of
computational capabilities.
A FE model of a representative Single Unit Truck (SUT)
was developed by the FHWA [2]. The model has been released to public use and
has been used for numerous computational studies of roadside hardware. The
model's primary purpose is to be used as a bullet object for computational
evaluation of road safety hardware, and as such it does not warrant the
complexity ordinarily employed in vehicle crash analysis models. In fact, too
much complexity in a bullet model may be detrimental to its primary purpose
because of an increased computational burden and structural failures in the
bullet that may overshadow the target's response. Therefore, possible
modifications of the vehicle model must always be evaluated within the context
of the roadside model development.
The objectives of this research were to conduct an
evaluation of the SUT model with respect to its ability to accurately simulate
its interaction with roadside safety hardware, to identify areas of possible
improvements based on comparison of simulations with crash experiments, and
consequently modify and update the model to improve its accuracy and take
advantage of current advances in FEM.
To be able to use the model efficiently and appropriately,
a prospective user has to understand its structure and modeling decisions made
during its development. The traditional user's manual format is not very
effective for describing a three-dimensional model, the interconnections
between different parts and their participation in different sub-modeling
entities. Therefore, a long lead-time is necessary for a new user to be able
to use the model with sufficient confidence to know that the perceived impact
configuration is indeed the modeled one. We have developed an interactive,
web-based User's Manual of this vehicle FE model to simplify this learning
process and make the model more transparent to new users.
This vehicle model is fairly well suited
to its purpose as a bullet vehicle. For example, on a 2-cpu 1.8 MHz. Dell
workstation with the Linux operating system, the truck-model-only run time
using LS-DYNA 970 [3] was 2 hours 40 minutes clock time to run 226 milliseconds
of simulation time. The nominal time step was about 4 microseconds. This appeared to be a
good trade-off between mesh refinement and speed.
Representative Single Unit Truck for
Roadside Hardware Analysis
Due to practical considerations in roadside hardware analysis, the
number of vehicle FE models used and developed is limited. The process
involves selection of a representative vehicle for each vehicle class, and
developing respective FE models. Therefore, the model and available
experimental data may not always coincide but it is assumed that the
differences in the structural behavior between models of the same class are
negligible with respect to the roadside hardware response and performance. The
Ford F800 Series Truck was selected as representative of the SUT vehicle class.
The available experimental data for the SUT category were obtained using a
variety of similar size trucks including; GMC, Chevrolet, Freightliner, and
International. The vehicle is ballasted to the correct weight for the test
level requirements.
A cursory inspection of several makes and
models of SUT's at a truck dealership revealed generally more similarities than
differences. The chassis were all parallel-rail frame types with front and
rear leaf spring suspension. They all had V-8 diesel or gasoline engines, and
all had dual-wheel rear axles. The cargo bodies are mounted on a series of
lateral C- or I-Beams which are welded to C-Channels that run parallel and
directly atop the chassis main frames. There typically is a wooden member as a
buffer between the Parallel C-Channels and the main chassis frame rails. Large
U-Bolts fasten the Cargo-body C-Channels to the chassis main rails. The GMC
7000 SUT used in the TTI test 7147-17 was typical of this design and had an
empty weight of 11470 lb. The NCAC F800 Model was also of this general design and had
an empty weight of 11051 lbs.
Outline of the SUT Model Analysis Process
The
analysis of the SUT model was conducted on evolving model versions as they were
being developed by NCAC. The initial analysis of the model resulted in several
suggestions and modifications that were subsequently implemented by the NCAC.
The evaluation of the early versions of the SUT model consisted of the
following steps:
- Preliminary evaluation of the SUT models using
FEM simulations
- Comparison of the simulations with the crash
experiments
- Identification of the model areas critical for
its performance in roadside hardware analysis
- Analysis of the SUT service manuals with respect
to FEM modeling approaches
- Analysis of the SUT model material models
- Analysis of the connectivity and joint models
- Analysis of the suspension and its possible
failure modes
- Model modification - analysis of the new results
and recommendations for updates in the model
The analysis and simulations of the early model
versions lead to recommendations for the model updates that were later
implemented by the original developers. The updated model was then used as a
platform on which the final analysis and modifications were performed.
SUT Material Models
Even the FEM models with large numbers of elements
will not be able to produce realistic results without realistically modeled
material behavior. One of the important areas of the SUT model update is the
implementation of more detailed material model assignment and material
properties. An exploded view of the SUT parts that are assigned materials is
shown in Figure 1.
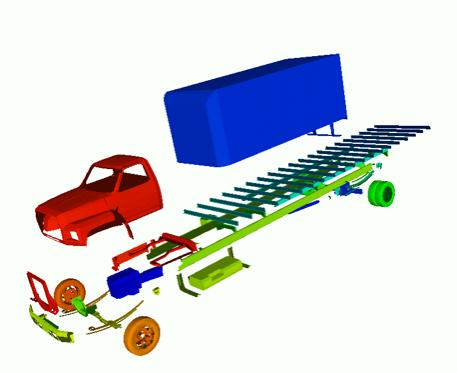
Figure 1
SUT computational parts
The vehicle is built on a main longitudinal rail
structure that acts as its backbone. It is therefore important to accurately
model the geometry and the material of the rails. The material of the rails is
specified in the Service Manual as the High Strength Low Alloy (HSLA) steel of
yield point 350 MPa. The material data available from the Auto/Steel
Partnership [4] and American Iron and Steel Institute [5] was used to enhance
the existing material model.
The new material model includes the effects of strain
rate sensitivity, which is very important in steels. Mild low-carbon steel
(DQSK) is primarily used in body structures and, by volume, constitutes the
largest part of the vehicle. The new model also adds a strain rate sensitivity
effect. Other significant material models implemented were the SAE 5160 bracket
and spring steel, SAE 1541 forged axle steel, Hot Rolled bumper steel and medium
Carbon alloyed SAE Grade 8 steel for nuts and bolts. Parts made of each of
these materials can be interactively viewed using the Virtual Reality Markup
Language (VRML) version of the documentation.
The most commonly used approach to modeling strain-rate
sensitivity of steels in automotive crash simulations is to use isotropic
plasticity models with a rate sensitivity component that has moderate
requirements on the experimental program. The types of material models that
are frequently used are the Johnson-Cook model [6], the Zerilli-Armstrong model
[7] and the piecewise linear strain rate sensitive material model [3]. The
models are appealing because they have been implemented in commercial codes
used for crash simulations and have a relatively small number of material
parameters that must be determined by experiments.
The most commonly used strain rate dependence material
model in crashworthiness simulations of steel structures is the piecewise
linear plasticity model. In this approach, effective strain-stress curves from
experiments are directly used in the computational material models and require
the least amount of effort for material model development. In simulations, for
a given rate of strain, the resulting stress in the plastic region is linearly
interpolated between the stress-strain values that were experimentally
determined in strain rate tests.
The computational model fits experimental data
exactly, but whatever testing artifacts or errors are contained in the
experimental data will be carried over to the simulations. The highest strain
rate in the experimental data acts as a saturation plateau for strain rate
effects. The strain rate dependent model for the HSLA 350 steel used in the
main rails of the SUT were developed by the Auto/Steel Partnership [4] and are
shown in Figure 2. The dashed curves show the results from the quasi-static
uniaxial tensile experiments.
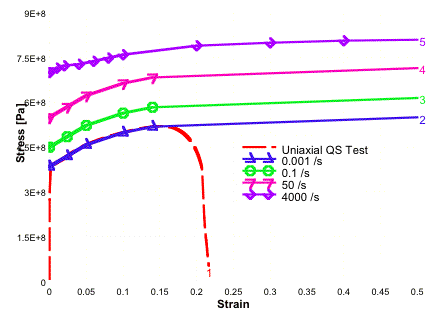
Figure 2
Material parameters for HSLA350
Vehicle – Infrastructure Asset
Interaction
An FHWA-funded study was undertaken by Battelle and ORNL to model
and assess different scenarios of truck vehicle run-off-road collisions with
roadway infrastructure elements, vehicle structural modes of failure, and
subsequent vehicle stability. The focus of this work was to identify areas of
the NCAC Ford F800 Single Unit Truck (SUT) model that was available at the time
that could be improved to make it more immediately useful as-downloaded from
the NCAC Finite Element Model archive. To accomplish this, Battelle worked
with Oak Ridge National Laboratory, the FHWA-sponsored National Crash Analysis
Center (NCAC) and other Centers of Excellence (COE) in Finite Element Crash
Analysis.
The vehicle model improvement study focused on impacts
with rigid barriers because this kind of test captures the vehicle model
behavior rather than the barrier response. Several simulations were run by
Battelle and ORNL during the course of this work and a number of vehicle model
improvements were suggested and implemented. The
procedure that was established to validate and verify the SUT model also will
provide the methodology for validation and verification of other heavy-vehicle
models currently under development at NCAC.
The experimental data collected on Single Unit Truck
(SUT) came from full scale tests performed by the Texas Transportation
Institute (TTI). The crash analysis simulations of the Texas Transportation
Institute (TTI) Crash Test No. 7147-17 – SUT impacting Single Slope
Concrete Bridge Rail, were performed. The crash test vehicle was an 18,000 lb.
GMC 7000 Single Unit Truck (11470 lb curb weight plus 6530 lb ballast load).
The vehicle was impacted into a single-slope bridge rail at 51.3 mph, at an
impact angle of 17.9 degrees
Figures 3 through 5 show (in very abbreviated form) of
the general level improvement achieved in this vehicle model's fidelity.
Figure 3 shows one snapshot in time (0.672 seconds after impact) from the crash
test experiment. Figure 4 shows the original vehicle model's response at 0.672
seconds after impact and Figure 5 shows the improved model's response at 0.672
seconds after impact.
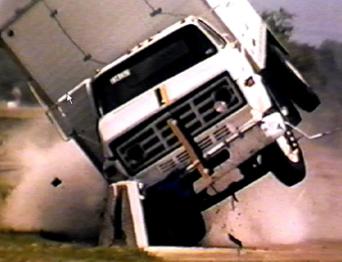
Figure 3
TTI Test at Time = 0.672 Seconds After Initial Impact
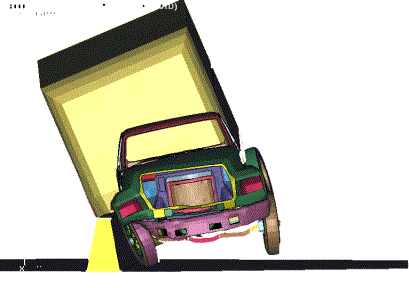
Figure 4 Original
F800 SUT Simulation at Time = 0.672 Seconds After Initial Impact
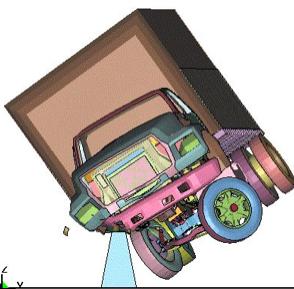
Figure 5
Improved F800 SUT Simulation at Time = 0.672 Seconds After Initial Impact
SUT Model Documentation
Vehicle
and roadside hardware FEM models from DOT and NCAC are available in public
domain so that they can be modified and combined with other models. The
availability of verified FEM models greatly facilitates research in the
transportation field. Perhaps the biggest obstacle in adoption of the FEM
models is their complexity and the respective startup time before they can be
confidently used in new impact scenarios. Since the computer simulations are
very tolerant to modeling errors, even the verified FEM models can be
inappropriately used if they are not fully understood.
Ever increasing computing capability leads to
correspondingly larger and more detailed FEM models so that the written
documentation cannot efficiently convey the model's structure and development
considerations and keep up with inevitable model updates. One of the
objectives of this research was to introduce new internet-based technologies to
the model documentation and presentation. The FEM vehicle modeling is
inherently complex and three-dimensional so the ability to effectively view the
model's information is very important.
To view the vehicle models, a combination of Virtual
Reality Modeling Language (VRML) and Hypertext Markup Language (HTML) was used
to build the Visualization Module of the documentation package. Additionally,
the Visualization Module allows for easy access of other tools within the
documentation package. Although new languages for three-dimensional computer
environments have been proposed, VRML with all its limitations is still
prevailing standard. A VRML file format is a plain text format that describes
the shapes and their properties within a 3D world. This file only specifies
objects and shapes within a virtual environment; it does not handle the
navigation and the interaction. Moving through the world, rotating objects,
and similar functions are handled through a VRML player, an application that
displays the VRML file.
Other important considerations are the size of model
documentation and the ability to efficiently transmit that information in
today's network environment. The dynamics of computing development will
inevitably lead to faster networks and better ways of model presentation, but
it is reasonable to expect that they will be based on three-dimensional modes
of data display. The VRML mode of interaction with the automotive
crashworthiness models was also explored in Reference [8] and briefly reviewed
below.
Vehicle geometry is converted into a VRML file by a
Perl script that sorts the parts, assigns them positions and rotations, colors
them, and assigns them appropriate behaviors. Due to this automated process it
is possible to quickly export new versions of the vehicle model to VRML format
and post them for viewing and analyzing on the World Wide Web. A virtual
control panel constantly follows the user inside the VRML world (Figure 6). The panel allows the user to select individual
vehicle parts, examine their mesh makeup, move, rotate, and eventually call up
an information page about the part and further cross-referencing as its
participation in different contact sets, element types, etc. The explode
feature separates the individual parts, allowing the user to get a good idea
about the interconnectivity of the vehicle (Figure 7).
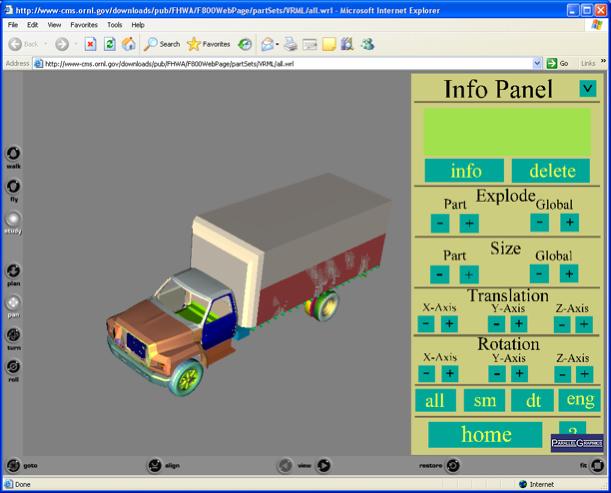
Figure 6
VRML Interface to the Documentation
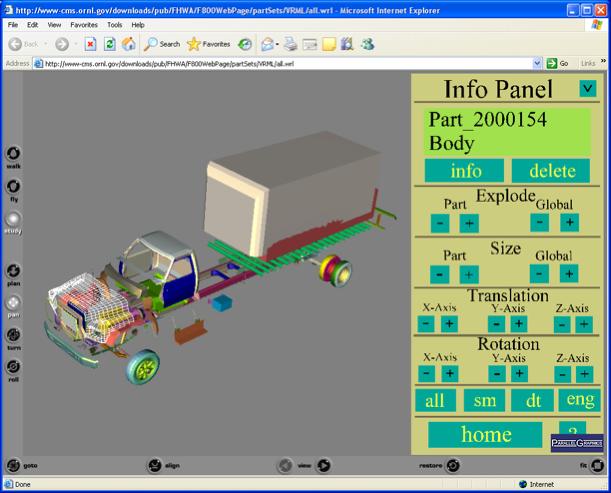
Figure 7
Exploded View with Selected Part
The name of the part and the subsystem it belongs to
are also displayed in the control panel. By using this control panel, the user
can easily navigate through the vehicle and gather information about it. The
delete function allows the user to remove any parts that are obstructing the
area of interest. This is a common occurrence - especially if user wants to
examine a cramped area such as the engine compartment. Additionally, the user
is able to examine a part's mesh composition by selecting it. These features
are easy to add, delete, or alter, due to the object-oriented design of the
VRML interface.
We
have organized the model documentation in 5 categories
- Part sets (subsystems)
- Parts
- FEM element types
- Material models
- Contacts
Other
groupings are clearly possible (i.e. connectivity models) and can be added to
the existing documentation.
The part sets categories are selected based on their organization
in SUT Service Manuals. The parts sets can be viewed in both HTML and VRML
modes. The HTML documentation is programmed as the staring point due to the low
data transfer requirement. As the user searches for more details, the VRML
interactive environment is offered to clarify the details of spatial
information.
SUMMARY
The main objectives of
this research were to conduct an in-depth evaluation of the Single Unit Truck
(SUT) finite element model with respect to its ability to accurately simulate
its interaction with roadside safety hardware and to identify areas of possible
improvements. The model's primary purpose is to be used as a bullet object
for computational evaluation of road safety hardware. The modifications of the
vehicle model were evaluated within the context of the roadside hardware model
development.
The analysis of the
model and comparison between simulations and tests lead to recommendations for
the SUT model modifications that were implemented by the original developers of
the model, National Crash Analysis Center (NCAC) and participants in this
project, Battelle, Oak Ridge National Laboratory and University of Tennessee.
The goal of the project was also to establish a methodology for validation and
verification of the finite element models used in roadside hardware analysis so
that it could be applied to other vehicle finite element models currently under
development.
The model and the
project developments are documented in an HTML based environment that allows
for dynamic visualization and interaction with the model. The user can view and
analyze all the main components of the model and their interactions. The goal
of the interactive 3D environment is to make the model more transparent to the
end users and to facilitate transfer of the developed models and technologies
to the end users.
Acknowledgements
This Heavy Vehicle Safety Research project was sponsored by the U.S.
Department of Transportation/Federal Highway Administration under
cooperative agreement #DTFH61-03-X-00030 with NTRCI.
Use of the supercomputers at
the ORNL Center for Computational Sciences (CCS) is gratefully acknowledged.
Our thanks to Roger Bligh of
the Texas Transportation Institute for his generous contribution of the
experimental test data that was essential to this study
Our thanks to
NCAC staff – Dr. Leonard Meczkowski, Dr. Dhafer Marzougui, and Dr.
Cing-Dao (Steve) Kan for their continuing support, help and advice on this
vehicle model.
References
1.
Belytschko,
T., Liu, W. K., Moran, B., Nonlinear Finite Elements for Continua and
Structures, Wiley, 2000.
2.
National
Crashworthiness Analysis Center Model Archive, http://www.ncac.gwu.edu/archives/model/index.html, 2003.
3.
Hallquist,
J. O., LS-DYNA3D, An explicit finite element nonlinear analysis code for structures
in three dimensions, LSTC Manual, 1995.
4.
Mahadevan,
K., Fekete, J. R., Schell B., McCoy, R., Faruque, O., Strain-Rate
Characterization of Automotive Steel and the Effect of Strain-Rate in Component
Crush Analysis, SAE paper 982392, 1998.
5.
Simunovic,
S., Shaw, J., Aramayo, G., Material modeling effects on impact deformation of
ultra light steel auto body, SAE Paper 2000-01-2715, 2000.
6.
Johnson,
G. R. and Cook, W. H., A Constitutive Model and Data for Metals Subjected to
Large Strains, High Strain-rates and High Temperatures, Proceedings of the
Seventh International Symposium on Ballistic, The Hague, The Netherlands, 1983,
pp. 541-547.
7.
Zerilli,
F. J. and Armstrong, R. W., Dislocation-Mechanics-Based Constitutive Relations
for Material Dynamics Calculations," Journal of Applied Physics V 61 (5),
pp. 1816-1825, 1987.
8.
Bobrek,
A., Simunovic, S., Aramayo, G., Collaborative Toolkit for Crashworthiness
Research HICSS-34, Minitrack on Developing and Deploying Collaborative Problem
Solving Environments 2001.