High Strain Rate Characterization of Mg Alloys
High Strain Rate Characterization of Magnesium Alloys
Srdjan Simunovic, Donald Erdman and J. Michael Starbuck
Oak Ridge National Laboratory
David Wagner
Ford Motor Company
1. Project Background
Low density and excellent machinability of Mg alloys make them good candidates for light-weight constructions of components in automotive industry. However, they also exhibit much more complex mechanical behavior than more common automotive materials. The mechanical response of Mg alloys involves notable anisotropy, non-isotropic hardening, yield asymmetry, lower ductility, and significant degradation of effective properties due to formation and evolution of micro-defects [7,15-18]. Accordingly, the necessary characterization procedures and constitutive models are more complex than commonly used uniaxial tests and isotropic plasticity. Another issue of concern for automotive designers is the strain rate sensitivity of various properties of Mg alloys. Preliminary tests indicate there is significant strain rate sensitivity of certain Mg alloys [1,7-14] (some were correlated to Al content), and it has a different character compared to steel materials [2, 3]. In Mg alloys, strain rate sensitivity is manifested by an increased hardening rate that is beneficial for diffusing and postponing the onset of localization and fracture. However, the lack of strain rate sensitivity information coupled with the lack of understanding of loading-induced property degradation for Mg alloys adds to the caution of using a new material. The strain rate sensitivity in Mg alloys is not only linked to yield strength but to other effective material properties such as effective elastic modulus, while internal structure evolution is important to the onset of ductile fracture. Experiments on several wrought and cast Mg alloys reported in the literature show considerable effect manufacturing [15, 16]. The correlation between properties of material in manufactured parts with specimens made under optimal conditions is needed if one wants to avoid lengthy testing for numerous manufacturing situations.
We are investigating rate-dependent properties of characteristic Mg alloys through advanced experiments and formulate the results in the framework of different modeling approaches such as continuum damage mechanics and mechanics of plastic voided solids. The experiments are conducted under various strain rates ranging from quasi-static to rates of 1000/s on the same equipment. The main scientific and technical advancement are: (1) the development of detailed information about Mg alloys response to impact loading, (2) characterization of property degradation by the control of imparted strain for high strain rates that allow for detailed investigation of evolution of internal state as a function of loading rate, (3) development of tightly controlled compressive and shear high-speed tests, (4) correlation of manufactured and ideal material properties. Advanced measurement techniques such as high-speed video and microscopy and X-ray are used. The deliverables for the project will be the documented rate sensitive properties for the selected Mg materials, microstructural characterization and damage data from the tests, and material model data for selected formulations.
2. Technical Plan
2.1 Task 1: High strain rate testing of Mg alloys
Three materials are evaluated for their strain-rate behavior; the AZ31 sheet alloy, the AM60B die cast alloy and the AM60B alloy from a thixomolded specimen. The AZ31 sheet alloy is supplied in a 2-mm thickness, whereas the two cast alloys are supplied in the form of 3-mm thick die-cast or thixomolded plates and samples cut out of the cast parts. To determine anisotropic material properties and yield asymmetry, tensile, compressive, and shear tests in principal material directions are needed. For example, material exhibiting orthotropic properties and yield asymmetry, such as Mg sheets and plates under monotonic loading, require test data for monotonic single loading paths, two directions of in-plane tension, in-plane compression, through-thickness tension, through-thickness compression and pure shear. When material also exhibits non-isotropic hardening, strain rate sensitivity, and ductile damage, as is the case with Mg alloys, the property measurements are usually not standardized and associated advanced models are implemented in commercial codes using user-supplied modules. Current testing capabilities at ORNL allow for full range of dynamic tests in tension and shear loading whereas compression can be currently only be conducted in quasi-static to low-strain rate mode. The setup for the high-speed compression in sub-Hopkinson regime will be developed using the reverse adapter similar to reverse cage system [4].
In the following subsection, high speed test configuration is presented in more detail. High-strain rate testing methods have been advancing in recent years [2, 3] in part due to the interest of exploiting strain rate effect in steels. However, test configurations in the sub-Hopkinson bar strain rate regime [4] (which covers the majority of the rates of automotive interest) has not yet been standardized, and are still under development [2, 3]. We believe that our configuration has numerous advantages with respect to loading control, data reduction and multiple source measurements and produces high-quality material data. Strain rates in split-Hopkinson bar tests are usually well above the automotive impact strain rates and, therefore, have limited applicability and are primarily for establishing an upper bound in stress response. Shear specimens recently proposed in the literature similar to Iosipescu specimen will be used for dynamic shear tests.
2.1.1 High Strain Rate Tests on Hydraulic Equipment
For tensile loading, variations of the dog-bone style tensile specimen configurations for sheet and solid material are used (see specimens from laboratories labeled B and C from Reference 3). Specimens are machined to accommodate a strain gage attachment in the load measurement section for sheet specimens. Testing for bar specimens from cast samples have similar arrangement. Figure 1 shows schematics for tensile sheet test from Reference 5.
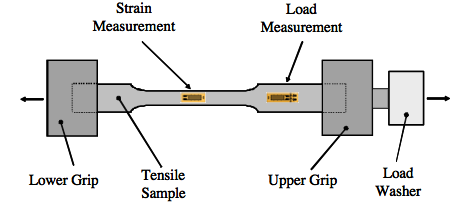
Figure 1. Tensile specimen configuration
Tests are conducted at 6 actuator speeds in order to achieve strain rates of quasi-static (0.001/s), 0.1/s 1/s, 10/s, 100/s, and maximum strain rates of the order of 500+/s. The machine allows for testing at speeds from quasi-static to 700 in/sec (18.5 m/s) over a range of 4 inches (100 mm) at maximum loads of 9000 lbf (40 kN). When an effective gage length for the chosen specimen is known the equipment can be programmed to run non-linear velocities in the drive file to achieve global strain control. Specimen gage lengths may need to be modified to provide sufficient time for specimen equilibration under the highest loading speeds [2,3,4]. A slack adapter is incorporated in the load train and itsŐ initial position controlled to allow the actuator to reach constant velocity prior to loading the specimen. Also, low mass grip concepts is utilized to minimize inertia effects and machine resonance on the measured specimen response. Measurement of forces, displacements, stresses and strains are based on the instrumentation listed below. Tests at rates higher than 1/s are recorded with high-speed video. To ensure consistency among the various test rates, several lower rate tests will be recorded during the test development.
Forces will be measured by:
1. Strain gage, full bridge DC load cell
2. Piezo-electric load washer
3. Calibrated strain gage on the specimen tab [5, 6].
Strains will be measured by:
1. Actuator displacement (temposonic acoustic displacement gage)
2. Digital Image Correlation measurements from high-speed video.
3. Strain gages located in the test gage region [5, 6].
The multiple measurements of both forces and displacements allow for correlation of the results and verification of the methods. A characteristic load-displacement curve for TRIP steel for various strain rates under tensile loading is shown in Figure 2.
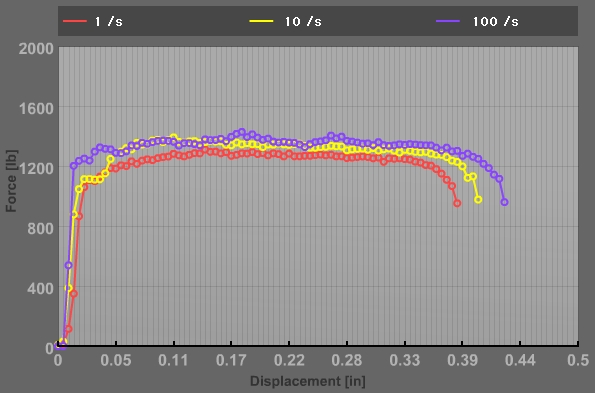
Figure 2. Steel specimen response at different rates
2.2 Task 2: Characterization of Damage Evolution in Mg Alloys
For realistic description of mechanical response and to characterize the onset of failure it is essential to identify and understand the initiation and progression of damage leading to material property degradation, instability and failure. To this goal, test methods must be able to incrementally load specimens to intermediate levels on the stress-strain curve and evaluate the magnitude of the damage evolution at each level. To accomplish this task at high strain rates it is necessary to employ novel fixturing to limit strain and/or load levels for a series of single specimens and evaluate the damage state employing microscopy/metallographic techniques on the sectioned specimens.
Figure 3 schematically depicts the method to induce a desired strain level at high rate into a specimen by attaching a strengthened pull rod that attached through a mechanical fuse to the bottom end of the specimen. The pull rod passes through a hole in the fixed plate and is attached to the test machine actuator. When the actuator moves downward, the specimen elongates until it contacts the fixed rigid plate and the mechanical fuse breaks and detaches from the specimen.
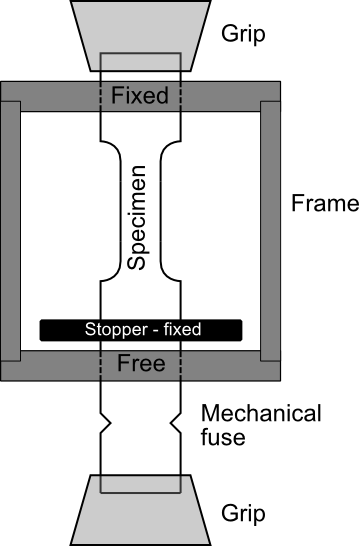
Figure 3. Strain Limiting Fixture Schematic
Investigation of material damage is assessed through measurement of effective elastic modulus, and measurement of evolving microstructural features (e.g. voids distribution and size) through combination metallographic and X-ray examinations. Evolving stages of damage (e.g. void nucleation, void growth and void coalescence) is characterized.
2.3 Task 3: Evaluation of Manufacturing Effect on Material Properties
Accounting for the as-manufactured material mechanical properties is an important aspect of material characterization, especially for lightweight metals such as Mg and Al. In cast material, these differences are the primarily result of micro and macro-porosity that occurs during casting. In Mg alloys, this porosity is manifested on macroscopic level in reduction of elastic modulus and fracture measures. In lightweight metals, creation of new surfaces via nucleation of voids and microcracks, their growth and coalescence plays central role in the mechanical response. Previous studies [7, 14] showed that Mg alloys are more prone to initiation and growth of microcracks leading to shear fracture compared to void nucleation, growth and coalescence which are the characteristic mechanisms of ductile fracture. Microcrack characterization is rather difficult, as it does not result in considerable changes of material volume in unloaded state. Non-Destructive Evaluation (NDE) of Mg specimens using X-rays and Computed Tomography (CT) are therefore very challenging [19] and require use of specialized equipment that surpasses resolution of commercially available X-ray CT devices. Optical microscopy on multiple cross-section planes [7, 20] have shown to yield reliable estimates in number density, size and distribution of microcracks as well as the initial porosity from casting. Similar to microporosity, microcracks are manifested on macroscopic level as a reduction in effective material properties. Mechanical degradation phenomena are usually modeled in the framework of continuum damage mechanics (CDM). The CDM uses internal state variables, called damage parameters, to describe influences of microscopic processes on the degradation of effective material properties. These damage parameters can often be used to establish equivalence between materials that have undergone different manufacturing and loading conditions. We propose to investigate materials made using different casting conditions and at several casting locations for the parts of interest, and to investigate and develop equivalence measures between them. This investigation is based on optical microscopy, interrupted strain tests and simulation [20]. The damage parameters and measures are usually investigated using the Bridgman specimens (notched bar and plate configurations) in order to determine the character and sensitivity of microscopic processes to different stress fields. Therefore, the standard coupon tests will be accompanied with Bridgman tests to investigate the effects of triaxiality and the premise of dominance of microcrack initiation and growth as governing mechanisms of damage and fracture in Mg alloys.
2.4 Task 4: Derivation of material property data for constitutive modeling
The experimental data for Mg alloys will constitute a large database for different loading situations and material property evolution. For constitutive models [21] of interest for Mg, it is necessary to plan the experimental program so that it would provide relevant information for the models. A simple example is measurement of void size distribution used in voided-solids plasticity models such as GursonŐs model and its derivatives. Localization models, failure criteria and cohesive zone models, based on local or non-local measures of stress and strain also require specialized interpretation of measured data in order to avoid severe mesh dependency during localization and failure, which can render computations meaningless, models must accounts for process zone dimension leading to fracture. The parameters for various constitutive models are derived from the experiments.
3. Project Milestones and Deliverables
The deliverables consist of the material characterization data, test procedures for determining rate-dependent material properties of Mg materials under different loading conditions, the associated text files and corresponding high-speed movies, data analysis (including microstructural characterization) and a web-based presentation of the results. A written Final Report documenting the experimental procedure and test results will be provided along with the raw data from each test in an ASCII file format.
The major milestone schedule is as follows:
Milestone Year 1: Determine high-strain rate properties for selected Mg alloys necessary to account for material anisotropy (multiple orientation), yield asymmetry (tension, shear, compression) and strain rate sensitivity. Develop compression and shear test setups for sub-Hopkinson speed loading regime (high-speed tests). During the initial phase (nine months) of the project we will investigate relative significance of high-strain rate on the macroscopic response. The project participants will review the results to refine the subsequent testing and analysis plans.
Milestone Year 2: High-strain rate properties for selected alloys with measurements of damage evolution with loading type (interrupted tests followed by microscopy and effective property tests)
Deliverables Year 3: Correlation between as-manufactured properties and cast plate specimens under controlled conditions (interrupted rate tests combined with microscopy and effective property tests)
4. References
1. Abbot, T., Easton, M., Song, W.; Mechanical behaviour of cast Magnesium alloys, Mat. Sci. Forum, v 419-422, p 141-6, 2003.
2. Recommendations for Dynamic Tensile Testing of Sheet Steels, International Iron and Steel Institute, 2005. http://www.worldautosteel.org/pdf_hsrt/DynTestingRecomPract.pdf
3. C. Wong, IISI-AutoCo Round-Robin Dynamic Tensile Testing Project, International Iron and Steel Institute, 2005. http://www.worldautosteel.org/pdf_hsrt/RptRndRobResults.pdf
4. Crenshaw, T. B., Boyce, B. L; Servohydraulic methods for mechanical testing in the Sub-Hopkinson rate regime up to strain rates of 500 1/s; Sandia National Laboratories, Report # SAND2005-5678, 2005.
5. D. Matlock, J. Speer, Constitutive Behavior of High Strength Multiphase Sheet Steels Under High Strain Rate Deformation, AISI/DOE Technology Roadmap Program, Report TRP 9904, 2005.
6. D.M. Bruce, Dynamic Tensile Testing of Sheet Steels and Influence of Strain Rate on Strengthening Mechanisms in Sheet Steels, Ph. D. Thesis # MT-SRC-003- 018, Colorado School of Mines, 2003.
7. El-Magd, E.; Abouridouane, M.; Characterization, modelling and simulation of deformation and fracture behaviour of the light-weight wrought alloys under high strain rate loading; International Journal of Impact Engineering, v 32, n 5, 2006, p 741-758
8. Yokoyama, T.; Impact Tensile Stress-strain Characteristics of Wrought Magnesium Alloys; Strain, v 39, n 4, 2003, p 167-175
9. Fjeldly, Alexander; Roven, Hans Jurgen; Effects of strain rate and anisotropy on the tensile deformation properties of extruded AlZnMg alloys; Journal Metallurgical and Materials Transactions A, v 31, n 3, 2000, p 669-78
10. Naka, Tetsuo; Hayakashi, Masanori; Nakayama, Yasuhide; Uemori, Takeshi; Kohzu, Masahide; Higashi, Kenji; Yoshida, Fusahito; Effects of strain rate and temperature on yield locus for AZ31 magnesium alloy sheet; Key Engineering Materials, v 340-341 I, 2007, p 119-124
11. Abu-Farha, Fadi K.; Khraisheh, Marwan K.;Deformation characteristics of AZ31 Magnesium alloy under various forming temperatures and strain rates; JOM, v 56, n 11, 2004, p 287
12. Abbott, T.; Easton, M.; Schmidt, R.; Magnesium for crashworthy components; TMS Annual Meeting, Magnesium Technology, 2003, p 227-230
13. Yokoyama, T.; Tensile and compressive properties of wrought magnesium alloys at high rates of strain; Journal De Physique. IV: JP, v 110, 2003, p 69-74
14. Oberhofer G., Dr. Lanzerath H., Wesemann J., Hombergsmeier E., Improved Plasticity and Failure Models for Extruded Mg-Profiles in Crash Simulations, 4th European LS-DYNA Users Conference, D - II - 29, 2003, ISBN 3-00-011175-1
15. Xiong, F.; Davies, C.H.J.; Anisotropy of tensile properties of extruded magnesium alloy AZ31; Materials Science Forum, v 426-432, n 4, 2003, p 3605-3610
16. Lee, Choong Do; Shin, Kwang Seon; Effect of microporosity on the tensile properties of AZ91 magnesium alloy; Acta Materialia, v 55, n 13, August, 2007, p 4293-4303
17. Lukac, P.; Trojanova, Z.; Hardening and softening in selected magnesium alloys; Materials Science and Engineering A, v 462, n 1-2, Jul 25, 2007, p 23-28
18. Zhou, Haitao; Liu, Liufa; Wang, Qudong; Lu, Da; Zeng, Xiaoqin; Ding, Wenjiang; Strain softening and hardening behavior in AZ61 magnesium alloy; Journal of Materials Science and Technology, v 20, n 6, December, 2004, p 691-693
19. Waters, A., H. Martz, K. Dolan, M. Horstemeyer, D. Rikard, and R. Green, Jr., Characterization of Damage Evolution in an AM60 Magnesium Alloy by Computed Tomography, Nondestructive Characterization of Materials IX, edited by R. E. Green, Jr., American Institute of Physics 1-56396-911-4, pp. 616-621 (1999).
20. Asim Tewari, Manish Dighe and Arun M. Gokhale, Quantitative Characterization of Spatial Arrangement of Micropores in Cast Microstructures, Materials Characterization, Volume 40, Issue 2, February 1998, Pages 119-132.
21. LeMaitre, J.; Handbook of Materials Behavior Models; Academic Press; 2001.